“品質林內”:與生命等價
? ? ? ? ? ? ? ? ? ?本文由 電器雜志 發表,轉載請注明來源!
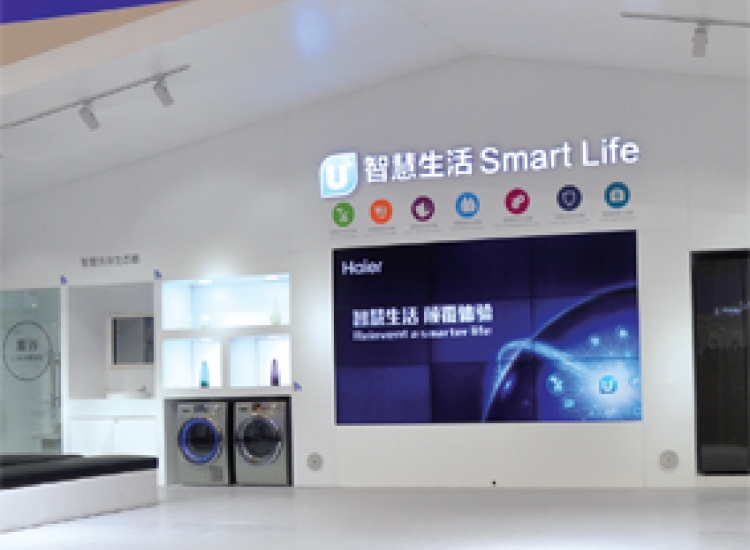
日本人對品質有著近乎神經質般的狂熱,看過紀錄片??《壽司之神》的人多數會有同感。為了保證壽司的完美品質,已經年近九旬的米其林三星廚師小野二郎對食材精挑細選,對壽司從制作到入口的每個環節的縝密計算,無不令人嘖嘖稱奇。如果客人覺得品嘗的壽司口感不佳,對于小野二郎來說,稱得上是一種奇恥大辱。
這種愛惜羽毛的榮譽感,在林內株式會社(以下簡稱林內)會長內藤明人心中則更加強烈,他將林內的產品品質視同生命。2017年1月20日,赴日參觀林內大口工廠和瀨戶工廠的《電器》記者看到,“品質就是我們的生命”??內藤明人的這句話被裝裱起來懸掛在廠區諸多的醒目位置,既像是一種激勵,也像是一種警示。而在整個參觀與交流之后,《電器》記者明顯感到,在林內全部經營與發展的思路背后,“品質就是我們的生命”這句話稱得上是最重要的理念和行為模式準則,堪稱林內企業經營文化的“靈魂”。
循環往復的“改善”
關于品質管理,林內也曾有過“灰暗的歷史時期”。“品質是我們的生命”這句口號的提出,其實源自許多年前的一個事故。“當時的林內還沒有建立起和今天一樣的品質觀,加上燃氣具產品比較特殊,是涉及煤氣、電及水的混合產品,安全性要求較高,產品技術條件也受到時代限制。在這樣的情況下,林內的燃氣熱水器產品發生過一起一氧化碳氣體中毒事件。”林內的一位有關負責人對來訪的《電器》記者十分坦誠。據他透露,這件事對內藤明人的觸動非常之大,他多次在公司內部強調林內生產的產品像飛機部件一樣,關乎人的生命。在此事件之后,林內立志再不能讓類似事件發生。自此,林內也將“零不良率”作為企業追求的目標。
《電器》記者注意到,林內對于品質的承諾并非空頭支票。為了達成“零不良率”這一目標,林內采取了大量行之有效的品質管理措施。首先,豐田汽車的生產管理系統聞名于世,與之同處日本制造中心愛知縣的林內也對其優秀的管理經驗進行了借鑒與學習。林內大口工廠生產管理課次長江口昌吾就告訴《電器》記者:“我們特意把豐田公司對生產系統管理有著豐富經驗的講師請到我們的工廠里來,對我們的相關領域進行指導和培訓。”
在日本企業的經營管理中,有個關鍵詞叫做“改善”,它是品質管理的基礎,也是最行之有效的方式。在林內,品質改善活動的數量之多,令記者感到吃驚。這些“改善”循環往復,已經成為林內日常生產過程中的“常態”。《電器》記者參觀時發現,無論在林內的大口工廠還是瀨戶工廠,關于品質改善活動的看板全部布置在生產車間里最顯眼的地方,改善的內容和成果,每個員工都能看到。“這樣可以激勵員工,誰做得好,誰還待努力,管理者對此也一目了然。”江口昌吾稱。
林內的這些品質改善活動從上世紀80年代開始就已十分活躍。每年,林內公司內部都會組成各種改善小組,公司幾乎所有人員都要參與,每個小組負責一個品質改善項目,并將改善結果在全公司范圍內進行發布,以提高林內整體品質管理的水平。
江口昌吾為記者舉例,林內的一個質量保證計劃QAP活動要求林內員工在實際的工作中,針對品質水平、工作現場標準化作業和生產線水平品質保證三個方面,不斷地尋找和發現問題,通過思考提出改善對策并實現標準化,然后進行效果檢查。“這項活動旨在每年將品質指標提升10%。” 江口昌吾說。
此外,在參觀大口工廠生產車間的過程中,《電器》記者還發現林內每月都在進行的一個改善活動??PDCA循環。江口昌吾指著看板上的內容,為《電器》記者答疑解惑,PDCA主要是針對生產線質量問題的改善活動,看板上方寫著這項活動的重要元素:短期計劃內容、執行計劃的負責人、問題發生在哪個時間段、計劃內容完成情況、應該采取的處理措施等。管理者每月都要檢查一次改善成果,并提出意見。每個員工都要分析并找出問題背后的原因,將成功經驗固化下去,并分享給其他人。
除了品質管理活動,林內還嚴格執行生產現場的標準化管理,即“3S、5定”制度,以減少無效工作量和施工錯誤。“3S”即整理、整潔、清掃,內容如字面含義,相對比較容易理解。“5定”為“定位”、“定品”、“定量”、“定姿”、“定時”:其中,“定位”是指每件物品都有固定位置,不能與其他種類混放;“定品”是每個零部件都有自己的號碼,不能混淆;“定量”是要確定好每件物品零部件數量;“定姿”是物品不能超出高度界限;“定時”是按時檢查現場情況。這些標準的評價工作流程,首先由各自工作負責人員自己確定評價分數,品保部部門長來檢查分數是否正確。此外,工廠長和副工廠長平時要巡回檢查,確定是否合格。
一道工序一道檢測
《電器》記者此次重點參觀的林內大口工廠成立于1964年,以生產燃氣灶、燃氣烤箱、洗碗機等廚房產品為主。工廠日產量在7400臺左右,生產型號達1733個。而林內在日本的另一個重要工廠??1979年建廠的瀨戶工廠,主要生產熱水器產品,年產量為90萬臺,產品型號超過1800個。
在型號眾多的情況下,想要保證每一件成品的品質并非易事。整體來看,林內的做法和原則是,給每一道生產工序都設置一個“檢查站”,用多重“保險”來避免不良品流向下一道工序。
在林內工廠的生產線上,每道工序的每件產品都要進行檢測,絕不存在“漏網之魚”。在大口工廠一條30米的生產線上,檢查裝置竟然多達40余個。在瀨戶工廠生產線參觀的過程中,記者也粗略統計了一下,檢查工序多達四十幾道。
并且,《電器》記者發現,林內生產線上的檢測機制已經實現高度自動化,先進檢驗裝置隨處可見。組裝線上多數機器都裝有FP裝置,用來檢測產品是否漏電、漏氣,有沒有明火,確保產品的安全和品質。不合格的產品通過時,警示燈會自動亮起。此時如果將不合格的產品放置在系統中向下一個步驟傳輸,生產線會自動檢測出不良品而停止工作。此外,在產品包裝環節,產品、說明書和紙箱的條形碼必須保持一致,否則銘牌無法打印出來。
即使有先進的品質檢測儀器,人眼檢測的作用仍不可忽視,這是林內品質檢測的“第二重保險”。林內集團執行董事、瀨戶工廠工廠長松本和彥坦誠地對記者表示,儀器檢測通常是看指定值能否達到標準,如果在其之后加一道人眼檢測的環節,才更加靈活、更加穩妥,保證萬無一失。”
在瀨戶工廠車間里每隔一段距離都會設有一個專門放置加工品的工作臺。松本和彥告訴記者,每天的上午、中午、下午都會有品質管理人員來檢查這些加工品,按檢查合格書逐項確認,相當于所有加工品的一次抽檢。而對于有些關鍵工序的加工品,松本和彥強調,每個小時都要進行一次樣品檢查。
同樣是在瀨戶工廠里,一個生產線放置的表格吸引了《電器》記者的注意力,瀨戶工廠副工廠長豬瀨洋志拿起它講解道,這標示的是品質管理部門的重點檢查項,告知檢查者這個步驟里需要重點目視檢查的內容,只有通過培訓的人才能在這里從事檢查工作。
此外,除了生產線上的嚴格檢測,林內產品還要經歷嚴苛的實驗室品質測試。據《電器》記者了解,林內研發的每一款產品都需送到日本總部的技術中心,進行長時間高強度的試驗,其中包括抗風、噴淋、抗鹽霧、抗電磁沖擊等多項測試。在風洞實驗室里,產品要經受風速達到40米/秒、相當于10級大風的考驗。
用“原廠自制”來捍衛品質
除了產品設計研發和生產制造過程中的精益求精,為了保證卓越的品質,如同《壽司之神》中小野二郎對食材的“挑剔”一般,林內在部件及選材方面十分“苛刻”,絕不會因為成本方面的因素而犧牲品質。
甚至為了保證產品整體的性能與品質,林內多年來一直堅持所有產品的關鍵部件采取原廠自制的模式。對于制造企業來說,原廠自制零部件的適配率肯定要比采購零部件高,質量和穩定性能更加可控,但是成本也同樣會提升不少。在權衡兩者之后,林內毫不猶豫地選擇前者,以此來捍衛“品質就是我們的生命”這一信條。
記者在林內的一份企業資料中看到,林內電磁閥、電子元件、燃燒器、感知器等重要零部件部件均為原廠研發自制。而專門負責研發制造這些零部件的相關企業包括RB控制株式會社、林內精機株式會社、株式會社柳澤制作所、林內科技株式會社、RT工程株式會社、株式會社燃氣所等。
此外,在參觀工廠的過程中,記者時不時就會發現,眼前的設備上貼有“Rinnai”標識的名牌。當記者帶著疑惑向林內集團執行董事、生產本部生產管理部部長井上一人詢問時,他告訴記者,這是林內的另一大“特色”:“我們一些比較關鍵和特殊的設備,都是由林內自己的技術人員開發制作的。還有些設備采取原裝訂購模式,即我們自己設計、制造零部件,由生產商按我們的要求組裝。這些設備與我們的產品生產配合度很高,會大大減少不良率。”
《電器》記者還了解到,在林內集團,負責這些自制設備統籌與研發的部門叫做生產技術部。這個擁有170名左右員工的部門,主要工作就是籌劃怎樣將新開發的產品進行生產轉化,思考這個過程中需要投入的各種元素。對原材料采購、成本控制、品質控制以及生產技術設備和專有模具的設計,甚至包括生產線的設計都要做到運籌帷幄。或許正是這些別具特色的‘獨門秘籍’,才能有如今消費者看到的林內產品出色的品質表現。
本文由 電器雜志 發表,轉載請注明來源!