解碼林內:熱能器具精品怎樣造?
? ? ? ? ? ? ? ? ? ?本文由 電器雜志 發表,轉載請注明來源!
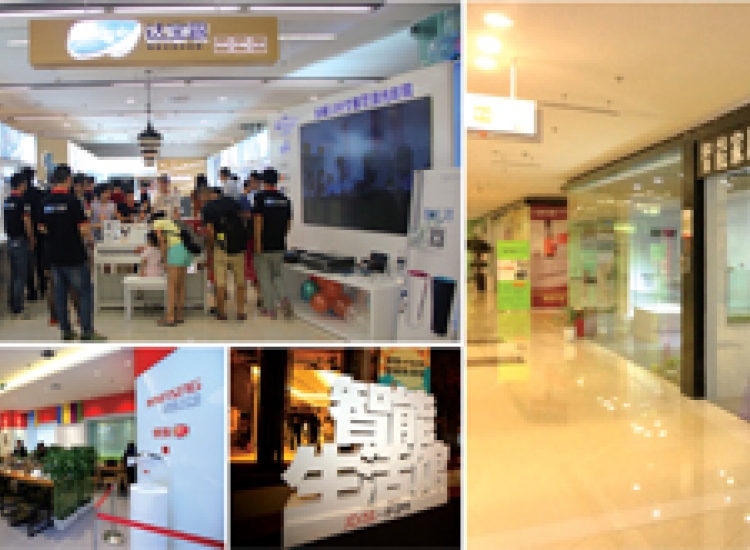
在全球的燃氣具產業界,林內享有盛譽,林內的產品是產業界“精工品質”和“精深技術”的代表。其中的原因,有林內近百年來專注燃氣核心技術的研發實力、對被奉為員工信條的“品質就是生命”的嚴苛堅守、卓越的人才培養機制,更有被業界推崇的“精密制造”生產體系。
2017年1月,《電器》記者走入林內大口、瀨戶兩大核心工廠,在探訪林內“工匠精神”的同時,也零距離去了解林內生產制造體系中的“精華”。
兩大工廠 管中窺豹
主要生產包括燃氣灶、燃氣烤箱、洗碗機等廚房設備的大口工廠,建于1964年,但《電器》記者走入這里時,卻絲毫看不出這已是一座使用超過50年的工廠。這座工廠制造的廚房設備營業收入占林內集團廚房設備總營業收入的75%,單日生產不同類型的產品合計7399臺,混流式生產全部型號數量高達1733個,而固定員工只有700人。
走入大口工廠的生產車間,“品質就是我們的生命”座右銘隨處可見,更令人震撼的是生產線上目不暇接的自動化裝置和設備,以極其緊湊的布局置放在各個工序環節,為數不多的工人周身放著眼花繚亂的零件和看板,而工人卻能有條不紊地以固定的速率、動作進行生產線操作。
在大口工廠,約有32臺沖壓機床,其中最大的一臺重量為1000噸,可以自制多種模具;約有28條鈑金生產線,上面大量采用全自動機器手進行焊接操作,而這些機器手的工裝設計全部由林內自己研發制造;在4條涂裝線上,林內自制的機械手完全模擬老工匠的操作手法對燃氣具格柵進行琺瑯操作;在21條總裝線中,大多是超過30米的連貫生產線進行柔性生產,每一道工序都采用自動檢查裝置進行自檢,過關后才能進入下一道工序,但這一過程卻看不到生產線的停滯;在生產線終端的打包裝箱環節,林內進行復雜但快捷的條形碼確認,產品、操作單和每個紙箱的條形碼必須一致才能裝箱。
為了對生產員工進行嚴格要求,大口工廠內設立了旨在培訓技能的“考工館”、旨在強調安全意識的“安全道場”,甚至連工人走路的速度都有指示燈來提示。除了生產設備之外,工廠內見到最多的是各種功能的看板,每道工序都有看板說明,每組生產團隊都有看板顯示成果,各種改善活動、質量檢驗活動也都有看板顯示。
在生產車間的情狀和管理方式上,主要生產熱水器設備的瀨戶工廠與大口工廠并無太大差別,所不同的則是生產線上的各種裝備。建于1979年的瀨戶工廠,年產能約為90萬臺,生產型號數量近2000種,固定員工僅為559人,其年營業收入約占林內熱水器國內營業收入總額的50%。
由于熱水器產品的燃燒器內置,因此在熱水器設備生產中,安全的重要性更高,生產管理的難度相對較大。但在瀨戶工廠,林內依舊通過精良的自制設備、極為繁復的檢測工序,將生產難度消解。走入瀨戶工廠的生產車間,可以見到同樣高強度的沖壓機,進行模具自制和自動更換;為了安全,設計了全自動化的熱交換器一體成型裝置;為了保證訂單的靈活性和豐富性,在表面處理工序設計的自動調色系統;在關鍵工序采用自動檢測之外,還要有具備資質的員工進行人眼觀察,確認產品沒有水等異物進入;在包裝環節采用激光打標機,在固定位置打標核準產品信息。
前述種種,僅僅是林內兩大工廠的一小部分,但反映出來的,卻是林內生產體系的重要特點:對品質至高無上地追求、靈活的自動化體系、具有核心技術的自制化裝備以及永不停歇的改善機制。
按需生產的自動化體系
在林內的大口工廠和瀨戶工廠內,《電器》記者注意到,同一生產線上不同型號的機器非常多,通常不同型號的機器因為要配置不同的零配件而無法順暢地混線生產,但在林內,“一臺產品的訂單也可以生產”卻是輕易就能高質量完成的事。不僅如此,小批量訂單的生產在林內的產量中占比極高。
據介紹,由于采用了加工、組裝、發貨在一個工廠進行的“一體生產體制”,實現了多品種混流生產,林內確立了可以應對快速交貨和大批量訂單的“3WAY體系”??這一體系分為三類??訂單生成當天或次日即可交貨的快速出貨產品、訂單生成三四天后出貨的菜單產品、訂單生成后約2周后出貨的大批量產品。在大口工廠,前兩類產品的產量占比超過95%,由此可見,“3WAY體系”的構建基礎,正是高效靈活的生產機制。
為了建立這樣高效靈活的生產機制的同時保證“零不良”的生產品質,林內需要高精尖的生產技術團隊配合開發、采購等各個部門進行生產線設計、改造,建立信息化管理、完善的自動化流程。據悉早在40年前,林內就已經開始了以條碼為主的生產線信息化建設,而早在上世紀80年代,林內就有了搬運機械手。到現在,任何一次新產品、新工藝的出現,林內均會以“生產技術部”為核心,從產品工藝開發的最初期就與各個部門協同,進行生產線的改造設計。據林內生產部門負責人舉例說:“比如一道工序設計節拍是40秒,那么生產線改造的基本條件就是保證這40秒節拍不受影響,在這一前提下實現工藝改造、檢測設備更新等操作。”
經過充分信息化、自動化設計的生產線令員工的操作便捷高效。以靈活的零部件裝取為例,在林內的工廠內,許多總裝線旁的工人身邊都擺放著不同規格的零件用于安裝,不同型號的產品傳送到位后,零件盛放裝置會以自動開蓋、自動亮背景燈等方式提示工人取件安裝,工人無需人眼識別就可以在極短的時間內完成復雜的挑揀過程。而在廠房的另一端,會有工人根據信息系統的數據去補充各種不同型號的零件到工位上,零件生產的供應商也會通過信息系統快速補充消耗的零部件。
為了充分保證自動化生產的高效率和零失誤,林內實施“3S/5定”??3S,即整理、整頓、清掃工程和作業區;5定,即定位、定姿、定量、定品、定時。其中,定位是每件物品都要有它固定的位置,不能與其他物品混淆;定品是每個零部件都有自己的編號,實現和產品一致;定量是每件物品都有確定的數量。這些都在確保林內的產品在混線生產中不出差錯,保證效率和品質。
事實上,保證靈活高效生產的自動化,極為重要的組成部分是生產線上高度匹配產品工藝的裝備及核心零部件,而這正是林內的又一法寶??高度自制化。
不可復制的高自制化
在林內集團的發展歷史上很早就確立的“零部件及裝備自制化”不僅成為林內完善生產體系的重要部分,更成為林內不可被復制的經典制造模式。
由于完全掌握“燃燒技術”“電子控制技術”“流體控制技術”等燃氣熱能器具的核心技術,林內在燃氣控制閥、電子控制元件、燃燒器、熱交換器等關鍵核心零部件上都實現完全自制。林內集團旗下除生產整機的工廠之外,還設有RB控制、林內精機等多個核心零部件制造公司,這些公司為林內提供專用的關鍵零部件的同時,也會為林內高效的生產工藝進行設計加工,這讓生產線組裝變得快捷和安全。
在零部件自制之外,林內依靠“生產技術部”的高科技研發實力,公司自己開發制作重要制造設備和金屬模具。在林內的工廠內,各種各樣帶有“Rinnai”標識的設備在運轉,這些用于模具沖壓、鈑金成型、焊接鉚釘、自動檢測等全部生產環節的專用設備,不僅完美匹配林內的生產工藝,更將林內生產的自動化水平逐步提高,也最大程度地提高了生產效率和品質。
此外,林內工廠中眾多的機械手在運轉,其中大部分機械手的工裝夾具和運動程序都是林內自己開發設計的。如前文提到的模仿老工匠的琺瑯機械手,就是林內自制自動化設備的科技成果。
由于大規模的自制化專用設備的使用,林內的生產模式幾乎不可復制,但林內并沒有在優勢上停步,而是將百年來的工匠文化繼續傳承,鼓勵員工對生產進行不斷地改善。
改善與傳承
林內集團執行董事、生產管理部部長井上一人在林內集團工作已經超過30年,其中大部分時間作為生產體系的管理者。他表示,30年來感觸頗深的,是林內生產自動化的大幅度升級,曾經工人經常加班的狀態不再出現,取而代之的是高效、高品質的生產。
事實上,林內在生產體系中的改善始終作為重要的環節在貫徹實施。在大口工廠車間中可以見到TPM(生產改善裝置)活動的看板,在瀨戶工廠中可以見到QLUP(生產質量改善)活動看板,每個工廠內都有細化到每個生產小組組員的生產改善看板。此外,林內還鼓勵員工自行設計“自動裝置”,在林內的“建設道場”,《電器》記者見到了無需電能、僅靠重力驅動的“端茶小木人”,還有僅靠滑輪和配重塊提供動力的收納支架。這些來自林內員工的發明創新已經有許多被應用到生產實際之中,如無需電能的自動收納支架就將此前員工彎腰擺放零件收納箱的動作取代,員工將收納箱擺放上去之后它會自動滑至低處。
此外,林內生產體系的自我改善還包括自制設備的改善。井上一人介紹說,雖然林內的自動化設備數量很多、自制率很高,但林內并不盲目使用自動化設備。以機械手為例,對于相對簡單的操作交給機械手,而多角度、相對復雜的操作仍然要由工人來完成。因此,林內自制的機械手等設備下一步改善的方向,則是“擬人化”,以實現難度更高的自動化操作。今后也會有更多如琺瑯機器人、鉚釘機器人一樣傳承工匠技術的機械手出現。
林內集團受訪的每一個人均表示,為了實現最高品質、向全世界提供創造舒適生活的熱能產品,林內仍會不惜代價進行包括生產體系在內的各種改善,將林內獨特的工匠文化,傳遞下去。
本文由 電器雜志 發表,轉載請注明來源!